New Talcing Process Improves Sheeting Quality
With technology constantly changing, it would be naive to turn a blind eye to new ways in which you can improve production processes which can help raise the quality of your products, regardless of your industry.
At Silicone Engineering, we had always used the more conventional way to talc our silicone sheeting which was a very simple process. An operator would apply talc onto the sheeting and a roller would then coat the sheeting evenly, as shown in the picture below. It was an effective process however very little control could be gained as to how much was applied and as we mentioned at the start, times and technology moves on. The silicone, especially coloured silicone would lose it’s true appearance due to a layer of talc covering it. Although not effecting the quality or performance, the company believed we could improve this stage of the manufacturing process significantly.
Talc, although necessary to stop the silicone sticking together in production, it can also cause inconvenience further down the supply chain with converters and fabricators as too much talc can effect machinery.
In light of this, Silicone Engineering set out to explore new technologies to improve our talcing process and made the decision to invest in the latest machinery (seen in picture below) to allow the talcing process to be thoroughly controlled with the beauty of tailoring talc coverage on customer demand. This gave a cleaner finish and a extra light even covering of talc.
To read more about our new talcing process and how this increased the quality of our sheeting, read our article in The Manufacturer which explains in detail our journey to install the state of the art talcing equipment.
http://www.themanufacturer.com/articles/new-talcing-option-to-improve-quality-at-silicone-engineering/
Flexible Silicone Solutions for the Rail Industry
The rail industry has seen vast improvements in both design and passenger safety over the last decade. Advanced interior designs using specialist materials allow rolling stock to become more efficient and more importantly, safer in operation.
Silicone lends itself to being used in a number of applications within the rail industry. Interior applications such as HVAC gaskets, lighting seals, door seals and silicone sheeting for vibration dampening highlights the versatility of silicone and its additional benefits that add to safety.
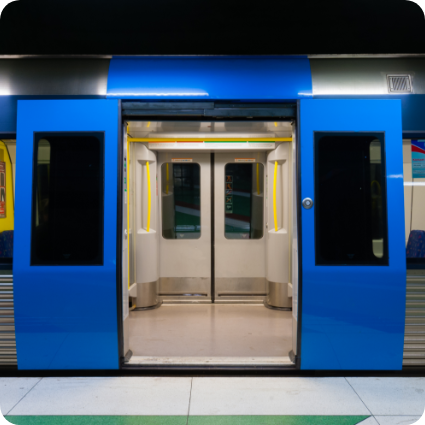
After the Kings Cross disaster in the 1980’s where toxic smoke was the main cause of fatalities, Silicone Engineering developed the LCH (low combustion hazard) silicone grade specifically for use in the mass transit industry, which when burnt produces low smoke and low toxicity emissions, therefore reducing risk of toxic fume inhalation. The LCH grade, available in solid and sponge, is now widely used in the rail industry to increase safety on board and like many other silicone products in our range, gives designers and engineers silicone solutions that add benefit to the end customer.
To find out more about how Silicone Engineering have transformed the rail industry with silicone solutions, read our latest article in Railway Strategies magazine by following the link below.
http://bit.ly/1eQ7qRu
Silicone Rubber in Aerospace
In an industry with no margin for error, reliable and high performing materials need to be used for the construction of aircraft. Silicone rubber’s versatile properties and its ability to withstand extreme temperatures makes it one of the ideal materials to use in the Aerospace industry.
Due to the fluctuation in temperatures experienced when aircraft are in operation, from hot temperatures on the ground to freezing temperatures at altitude, materials (in this case silicone rubber) need to be able to cope with such change without compromising performance. Silicone Engineering’s silicone materials are stable up to +230°C and go down to -60°C with our high temperature formulas able to withstand +270°C. This stability across a wide range of temperatures gives confidence that silicone seals and gaskets within the aircraft will not degrade or fail, which is vital for safety.

Silicone Engineering’s materials have been used in the aerospace industry for many years and our experience and knowledge has been built up throughout the company’s 55 years.
To read more about silicone within the aerospace sector take a look at our recent editorial in Aerospace Manufacturing magazine by following the link below.
http://www.aero-mag.com/features/38/201411/2819/